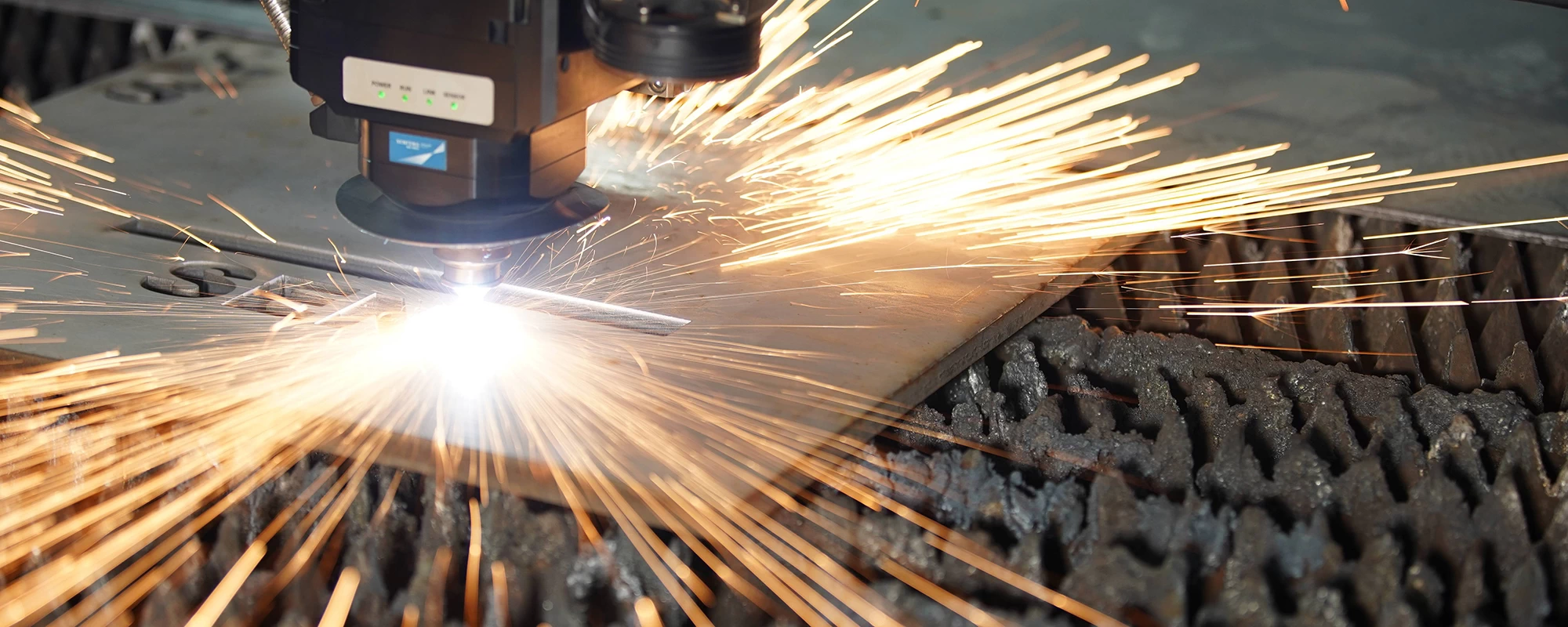
Beim Faserlaserschneiden von Metallplatten kann der Laserstrahl durch seine hohe momentane Temperatur das Metall leicht durchtrennen. Doch eine übermäßige Hitzeeinwirkung kann zu schlechter Schnittqualität führen. Beispielsweise kann beim Schneiden dicker Platten, die Hilfsgase erfordern, ein zu hoher oder zu niedriger Gasdruck eine übermäßige Wärmeeinbringung verursachen, die Schlackenbildung begünstigt. Ähnlich kann es beim Schneiden kleiner runder Löcher durch den begrenzten Raum für die Wärmeausbreitung zu einer konzentrierten Wärmeanreicherung kommen, was ebenfalls leicht zur Schlackenbildung führt.
Verschiedene Kunden haben unterschiedliche Anforderungen an die Qualität der Schnittoberflächen und den Verarbeitungsgrad. Wenn Schlackenbildung auftritt, können folgende Schritte zur Fehlerbehebung und Anpassung unternommen werden:
01 Überprüfung der Ausgangsleistung
Beim Laserschneiden, führt eine zu geringe Ausgangsleistung dazu, dass der Schnitt unvollständig oder gar nicht erfolgt, was zu Schmelzflecken und Narben an der Schnittkante führt. Ist die Leistung jedoch zu hoch, wird der Schnittspalt zu groß, und eine hervorragende Schnittqualität kann nicht erreicht werden.
Die folgende Abbildung zeigt die Probleme, die beim Schneiden von Baustahlplatten auftreten, wenn die Laserleistung nicht ausreicht.
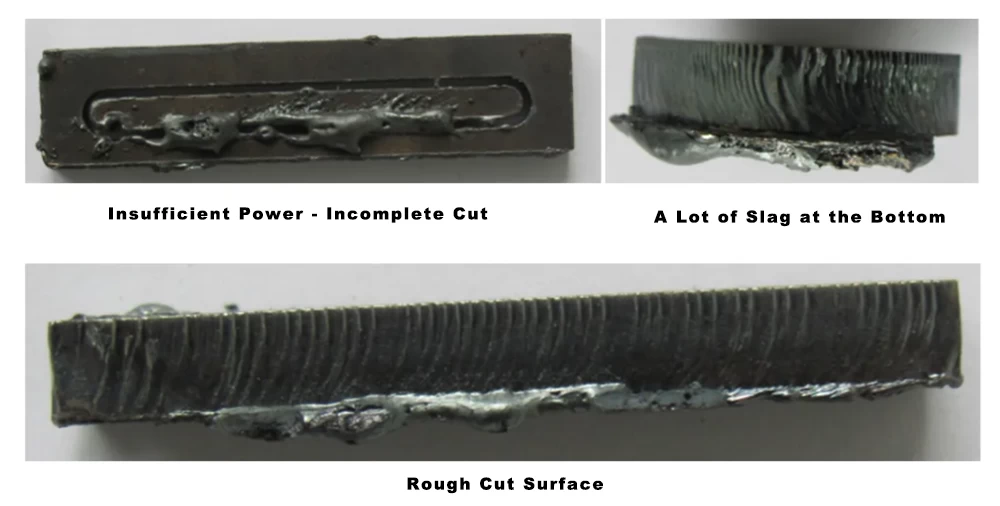
02 Überprüfung des Gasdrucks
Beim Laserschneiden werden Hilfsgase (häufig O₂, Druckluft, N₂ und Edelgase) verwendet, um geschmolzene Schlacke wegzublasen und die Wärmeeinflusszone während des Schneidens zu kühlen.
Die meisten Metalle werden mit aktiven Gasen wie O₂ verarbeitet, da O₂ die Metalloberfläche oxidieren und so die Schneideffizienz verbessern kann. Ist jedoch der Hilfsgasdruck zu hoch, entstehen auf der Materialoberfläche Wirbelströme, die die Entfernung des geschmolzenen Materials erschweren, wodurch der Schnitt breiter und die Schnittfläche rauer wird. Ist der Druck zu niedrig, kann das geschmolzene Material nicht vollständig weggeblasen werden, was dazu führt, dass Schlacke an der Unterseite des Materials haften bleibt.
03 Überprüfung der Fokusposition
Die Fokusposition bezeichnet den Abstand zwischen dem Laserfokus und der Oberfläche des Werkstücks. Sie beeinflusst direkt die Rauheit der Schnittfläche sowie die Neigung und Breite des Schnitts.
Liegt der Fokus zu weit vorne, wird mehr Wärme vom unteren Teil des Werkstücks aufgenommen. Bei konstanter Schneidgeschwindigkeit und konstantem Gasdruck können das geschmolzene Material und das Material in der Nähe der Schnittfuge als Flüssigkeit auf die Unterseite fließen. Nach dem Abkühlen bildet das geschmolzene Material kugelförmige Schlacken an der Unterseite. Liegt der Fokus zu weit hinten, wird weniger Wärme vom unteren Teil des Materials aufgenommen, was dazu führt, dass das Material nicht vollständig schmilzt und scharfe, kleine Schlacken an der Unterseite haften bleiben.
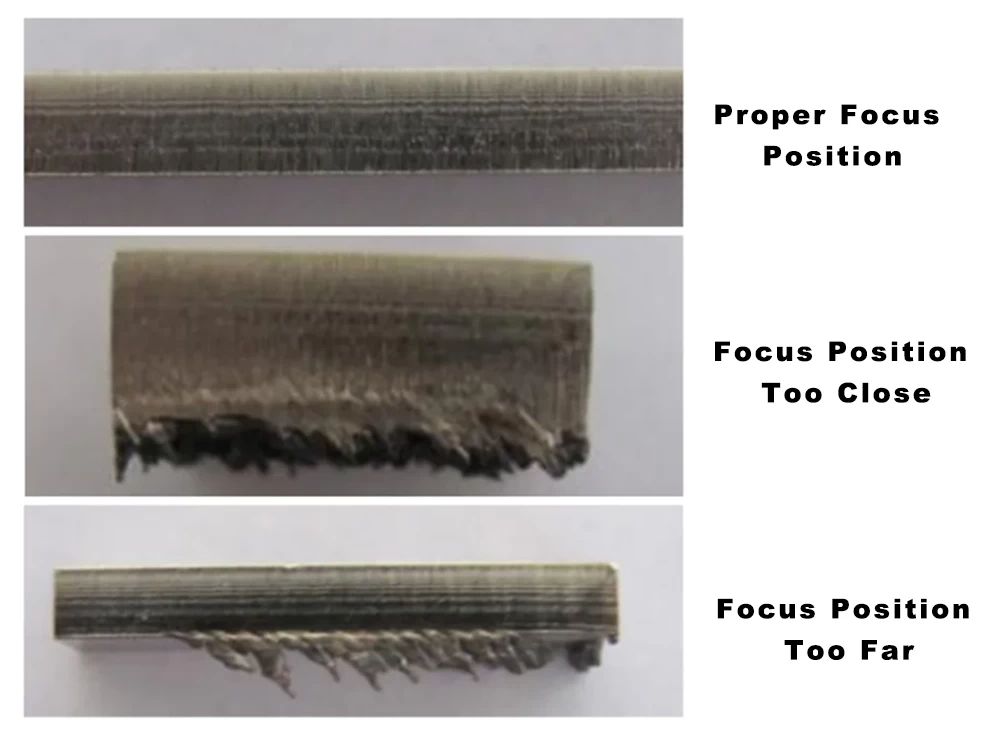
04 Überprüfung der Schneidgeschwindigkeit
Die Schneidgeschwindigkeit beim Laserschneiden wird durch das Material und die Dicke der Platte bestimmt. Die Wahl der Schneidgeschwindigkeit hat großen Einfluss auf die Schnittqualität. Die richtige Geschwindigkeit verbessert sowohl die Schneideffizienz als auch die Qualität.
Eine falsche Schneidgeschwindigkeit kann Schneidfehler verursachen, wie in der untenstehenden Abbildung dargestellt:
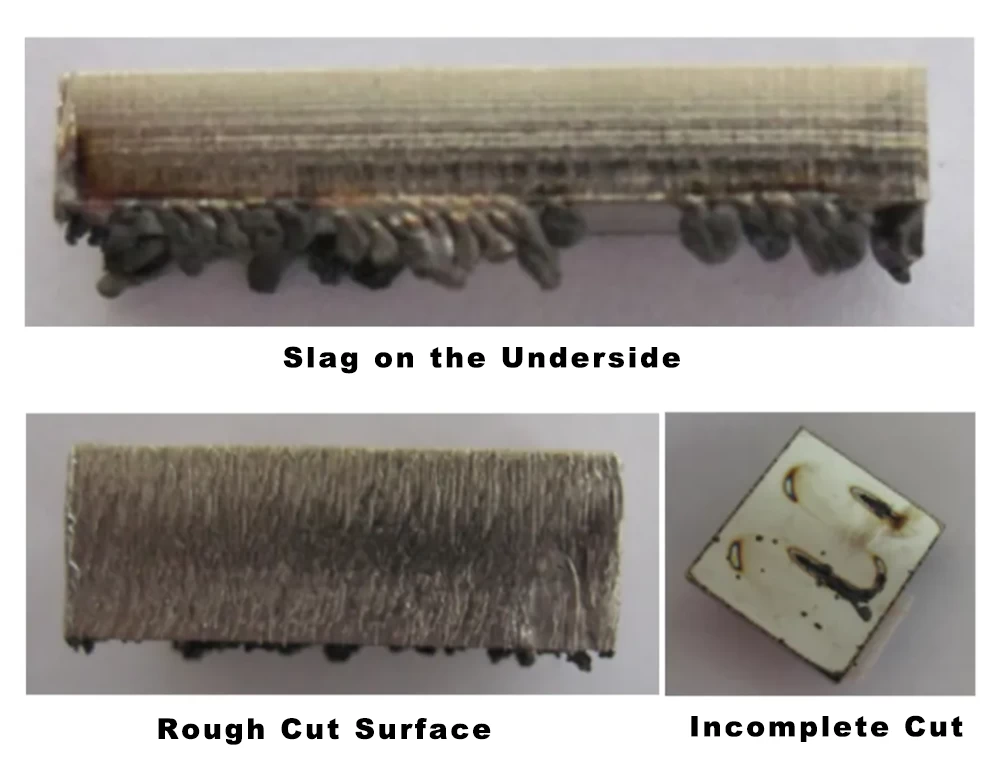
Fazit
Schlackenbildung ist ein häufiges Problem beim Laserschneiden, das die Schnittqualität beeinträchtigt. Durch die Anpassung von Ausgangsleistung, Gasdruck, Fokusposition und Schneidgeschwindigkeit kann die Schlackenbildung wirksam vermieden oder minimiert und die Schneidleistung sowie -effizienz verbessert werden. Während der Fehlerbehebung sollten alle Faktoren angepasst werden, um eine optimale Schneidqualität zu gewährleisten.
Teilen Sie den Beitrag jetzt:
Das könnte dir auch gefallen
Yupec Laser ist ein führender Anbieter von Raycus-Faserlasern in Europa, mit Fokus auf Verkauf, technischer Unterstützung und Service.
Mit jahrelanger Erfahrung und einem Team aus Branchenexperten helfen wir Ihnen gerne bei allen Ihren Laser- und Laseranwendungsbedürfnissen.
Für mehr Informationen zu unseren Produkten und Services kontaktieren Sie uns bitte. Wir freuen uns auf eine Zusammenarbeit und gemeinsame Innovationen.